Herkömmliche Instandhaltungskonzepte werden den heutigen Anforderungen nicht mehr gerecht: Sie binden Kapital und verbrauchen zu viele Ressourcen. Eine Lösung heißt Predictive Maintenance. Doch bisher setzen nur wenige Unternehmen auf diese Option.
Ein Großteil der Unternehmen weiß um die Chancen, die vorausschauende Instandhaltung bietet. Das ergab eine Umfrage der Unternehmensberatung BearingPoint unter 74 Unternehmen aus den Bereichen Maschinenbau, Chemie/Pharma und der Automobilindustrie. Den Nutzen sehen 80 Prozent der Befragten in der Erhöhung der Anlagenverfügbarkeit, 60 Prozent erhoffen sich sinkende Wartungskosten. Trotzdem mangelt es noch an der Umsetzung: Während sich 84 Prozent der Befragten mit dem Thema Predictive Maintenance in ihrem Unternehmen auseinandersetzen, hat nur jedes vierte Unternehmen bereits erste Projekte durchgeführt.
Evaluation lohnender Bereiche. Wie können Mittelständler herausfinden, ob sich Predictive Maintenance auch für ihr Unternehmen lohnt? Die Antwort liefert die Auswertung eigener Service-Daten. Sie verraten, bei welchen Maschinen, Geräten oder Anlagen häufiger Probleme auftreten. Dabei gilt es zunächst, Bedienfehler von technischen Schwierigkeiten zu trennen. Denn nur im zweiten Fall kann Predictive Maintenance greifen. In Bezug auf die technischen Auffälligkeiten sollte dann eine Nutzen-Kosten-Betrachtung folgen: Welchen Preis haben bisherige Ausfälle, welche ließen sich durch vorausschauende Wartung vermeiden und was hieße das unter dem Strich?
Fällt diese Rechnung zugunsten von Predictive Maintenance aus, geht es an die ersten Überlegungen zur Umsetzung. Dabei sind fünf wesentliche Punkte zu beachten: Datenmaterial, Analysen, Visualisierung, durchgängige Prozesse und Vernetzung.
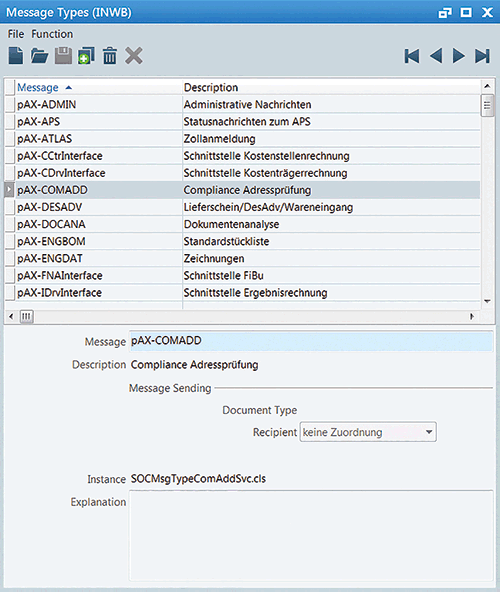
Abbildung 1: Nachrichtentypen im standardisierten pAX-Nachrichtenformat.
Datenmaterial – vieles liegt bereits vor. Die Basis für vorausschauende Instandhaltung sind selbstverständlich aussagekräftige Daten. Diese liegen im Unternehmen oft bereits vor: So sind viele Maschinenparks, Produktionsanlagen und Betriebsmittel heute mit Sensoren ausgestattet. Für die Bestimmung des richtigen Wartungszeitpunkts gibt es weitere lohnende Quellen: Wetterstationen liefern beispielsweise Informationen zu Wind- und Temperatureinflüssen, Vereisungen oder Blitzschlägen, die für Außenanlagen wichtig sein können.
Schließlich ist auch das Timing noch zu betrachten: Wie schnell stehen die Daten zur Verfügung und wie rasch können sie ausgewertet werden? Wachsen sich Änderungen blitzartig zu Krisen aus, ist Echtzeitdatenmanagement nötig. Handelt es sich eher um schleichende Prozesse und Abnutzungen, geht es auch ohne. In jedem Fall sollte das Hauptaugenmerk auf der Datenqualität liegen, um richtige Schlussfolgerungen ziehen zu können.
Auswertung – vom Algorithmus bis zur Modellierung. Im Mittelpunkt aller Bemühungen steht die Frage nach dem optimalen Wartungszeitraum. Je später oder seltener gewartet wird, desto stärker steigt das Risiko eines ungeplanten Ausfalls. Eine zu frühe Wartung – und damit eine hohe Wartungsfrequenz – reduziert jedoch die Verfügbarkeit der Maschinen.
Beiw dieser Gratwanderung setzt Predictive Maintenance auf Algorithmen, um Trends in Daten zu erkennen und mögliche Ausfälle vorherzusagen. Auch Analysen – etwa zur lastabhängigen Zuverlässigkeit oder Verschleißmodelle – fließen in die intelligenten Vorhersagen ein. Für diese Modelle wird auch auf historische Daten zurückgegriffen. Außerdem müssen Parameter definiert werden, deren Überschreitung weitere Aktionen auslöst. Menschliche Erfahrung ist hierbei der Schlüssel, um die richtigen Schwellwerte festzulegen.
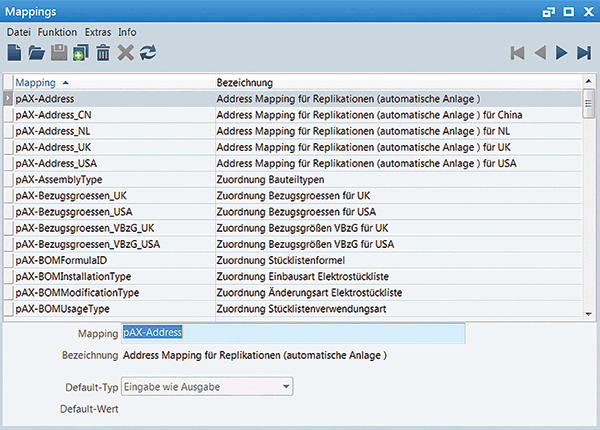
Abbildung 2: Mapping für Umrechnungen und Konvertierungen im Zielsystem.
Leichter und schneller entscheiden durch Visualisierung. Unverzichtbarer Baustein jeder Predictive-Maintenance-Lösung sind Visualisierungsmöglichkeiten. Denn auch bei der vorausschauenden Instandhaltung spielt der Mensch eine zentrale Rolle. Er ist nicht nur bei der oben erwähnten Definition von handlungsauslösenden Grenzwerten gefragt, sondern auch bei Überwachung und Reporting. Zudem muss er in allen Prozessen, die (noch) nicht vollautomatisch ablaufen, die nötigen Entscheidungen treffen. Dabei erleichtert eine visuelle Darstellung die Urteilsfindung deutlich.
Durchgängige Prozesse schaffen Rentabilität. Effizienzgewinne durch vorausschauende Planung sind indes nur auf der Basis gut verzahnter Prozesse möglich. Wird also ein Event festgestellt, müssen auch nachfolgende Aktivitäten möglichst automatisiert vorbereitet werden. Dazu bedarf es einer ERP-Lösung als digitaler Drehscheibe, die verschiedenste Funktionalitäten und Systeme verknüpft. Die Vernetzung verschiedenster Anwendungen und Einheiten ist dabei längst nicht so schwierig, wie gemeinhin angenommen. Speziell auf die Bedürfnisse des Mittelstandes eingerichtet ist beispielsweise die Integration Workbench von proALPHA. Ihr Enterprise Service Bus bietet so eine Integrationsplattform. Und nur ein integrierter Workflow garantiert die nötige Rentabilität von Predictive Maintenance.
Vernetzung auf allen Ebenen. Fertiger sollten jedoch nicht nur an die Vernetzung ihrer eigenen Systeme und Prozesse denken. So gilt es beispielsweise, externe Servicepartner einzubinden – wichtig, wenn Wartungsleistungen nicht vom eigenen Team erbracht werden. Gleiches gilt für Lieferanten von Ersatzteilen, die ein Fertigungsbetrieb nicht selbst erstellt und bevorratet. Predictive Maintenance auf der Basis eines leistungsfähigen ERP-Systems durchdringt also auch die Supply Chain.
Profitieren können Fertiger außerdem von der Zusammenarbeit mit Gleichgesinnten. In größeren Organisationen bieten sich bereichsübergreifende Innovationsteams an, um sich gegenseitig zu motivieren, auf dem aktuellen Stand zu halten und mit neuen Ideen und Impulsen zu versorgen. Auch die Vernetzung mit Verbänden und der Austausch mit Partnern helfen, den Know-how-Transfer zu beflügeln. Wer Wissen und Erfahrungen teilt, kommt schneller voran und kann Vorteile schneller umsetzen. Eine Win-Win-Situation für alle Beteiligten!
Fazit. Die Vorteile der vorausschauenden Wartung sind vielschichtig. Indem sie ungeplante Ausfälle verhindert, lassen sich zahlreiche Produktionskostensteigerungen umgehen. Denn teurere Ersatzkapazitäten aus der verlängerten Werkbank oder weniger produktive Ersatzmaschinen müssen nicht ungeplant abgerufen werden. Weil Ausfall- und Instandsetzungszeiten gezielter geplant werden können, steigt auch die Produktivität. Denn die Wartungstermine können betriebliche Rahmenfaktoren wie etwa Wochenenden oder Werksferien berücksichtigen. Unnötige Kosten für Routinewartungen entfallen. Und last but not least leben gut gepflegte Maschinen einfach länger und liefern länger hohe Qualität.
Dr. Markus Berg,
Leiter Softwareentwicklung Produktion
bei proALPHA
Illustration: © Botond1977/shutterstock.com
Predictive Maintenance & Co.: Türöffner für positive Customer Experience
Predictive Maintenance: Maschinenverfügbarkeit rauf, Kosten runter, Kundenbindung nachhaltig stärken
Hybride Wartungsmodelle für Server und Storage – Third-Party Maintenance als Alternative